중공드릴의 도입과 응용전망
중공 드릴 비트(코어 드릴이라고도 알려진 다중 모서리 강판 드릴)는 다중 모서리 원형 절단을 위한 효율적인 드릴 비트입니다.드릴링 직경은 12mm에서 150mm까지입니다.그들은 주로 철강 구조 엔지니어링 및 철도 운송과 같은 철강 부품을 드릴링하는 데 사용됩니다., 교량, 선박, 기계 제조, 항공 우주 및 기타 홀 가공 분야에서 드릴링 성능이 전통보다 훨씬 뛰어납니다.높은 드릴링 효율, 가볍고 노동력을 절약하는 드릴링, 다날 강판 드릴 및 자석 시트 드릴의 특성을 지닌 양날 트위스트 드릴 매칭 공구는 대형 공작물의 다방향 드릴링을 수행할 수 있습니다.작업이 편리하고 유연하여 건설 시간을 효과적으로 단축하고 현대 강철 부품의 드릴링 및 환형 홈 가공을 위한 첫 번째 선택 도구가 되었습니다.
1.절단에 미치는 영향Edit Bro광고?
중공 드릴 비트는 휴대용 도구에 더 적합한 구멍 처리 도구입니다.그러나 중공 드릴은 제조 공정이 상대적으로 복잡하고 막힌 구멍을 가공할 수 없기 때문에 금속 절단에는 일반적으로 사용되지 않습니다.일반적으로 직경이 큰 구멍이나 귀금속 공작물을 가공할 때 또는 드릴링 장비의 성능이 제한적인 경우에만 사용됩니다..거기부터중공 드릴 비트에 대한 표준 제품이 없기 때문에 특수 재료 가공에 사용되는 대부분의 중공 드릴 비트는 자체 개발해야 합니다.
후면 각도 ef완벽하다
2.갈퀴의 효과절삭력에 대한 각도?
경사각의 변화는 칩 소재의 변형 정도에 영향을 미쳐 절삭력의 변화를 가져옵니다.g칩 변형이 커질수록 절삭력이 커집니다.칩 변형이 작을수록 절삭력도 작아집니다.경사각이 0°~15° 범위에서 변경되면 절삭력 보정 계수는 1.18~1 범위에서 변경됩니다.
3.경사각의 영향드릴 비트의 내구성에 대해?
드릴 비트의 경사각을 높이면 공구 팁의 강도와 방열량이 감소하고 공구 팁의 응력에도 영향을 미칩니다.경사각이 양수 값이면 공구 끝이 t의 영향을 받습니다.o 인장 응력;경사각이 음수 값이면 공구 팁에 압축 응력이 가해집니다.선택한 경사각이 너무 크면 드릴 비트의 날카로움이 증가하고 절삭력이 감소할 수 있지만 공구 팁의 인장 응력이 커지고 공구 팁의 강도가 감소하며 쉽게 깨지게 됩니다.절단 테스트에서 과도한 경사각으로 인해 많은 드릴 비트가 손상되었습니다.그러나 가공할 소재의 경도와 강도가 높고 휴대용 드릴링 장비의 메인 샤프트와 기계 전체의 강성이 낮기 때문에 선택한 경사각이 너무 작으면 드릴링 중 절삭력이 증가합니다. 메인 샤프트가 진동하게 되고 가공된 표면에 뚜렷한 진동이 나타납니다.드릴 비트의 내구성도 감소됩니다.
5. 절단 성능에 대한 효과ce
여유각을 늘리면 측면 표면과 절삭 재료 사이의 마찰을 줄이고 가공된 표면의 압출 변형을 줄일 수 있습니다.그러나 여유각이 너무 크면 bl강도와 방열 능력이 감소됩니다.
여유각의 크기는 드릴 비트의 내구성에 직접적인 영향을 미칩니다.드릴링 과정에서 드릴 비트의 주요 마모 형태는 기계적 긁힘과 상변화 마모입니다.기계적 마모 및 마모를 고려하면 절단 수명이 일정한 경우 여유각이 클수록 절단 가능 시간이 길어집니다.위상 변화 마모를 고려하면 여유각이 증가하면 방열 능력이 감소합니다.드릴 비트의 종류.드릴 비트가 마모된 후 측면의 마모 영역이 점차 넓어지고 절삭력이 점차 증가함에 따라 마찰에 의해 발생하는 열이 점차 증가하여 드릴 비트 온도가 상승하게 됩니다.온도가 드릴 비트 상전이 온도까지 상승하면 드릴 비트가 빠르게 마모됩니다.
6.샤프닝 효과프로세스
중공 드릴 비트는 더 적은 수량을 사용하고 처리 배치가 작습니다.따라서 드릴 비트를 설계할 때 가공 기술 문제를 고려해야 하며, 가공 및 샤프닝은 가능한 한 일반적인 가공 장비와 일반적인 도구를 사용하여 이루어져야 합니다.칩 흐름 성능.유출 과정에서 칩은 경사면에 의해 압착되고 마찰되어 칩이 발생합니다.추가 변형.칩 바닥의 금속이 가장 많이 변형되어 경사면을 따라 미끄러지면서 칩의 바닥 층이 길어지고 다양한 컬링 모양이 형성됩니다.중공 드릴 비트를 사용하여 구멍을 뚫는 경우 칩 제거를 용이하게 하기 위해 칩을 칩이나 스트립으로 절단하는 것이 좋습니다.가공 및 샤프닝을 용이하게 하기 위해 경사면은 칩 브레이커 없이 평평한 표면으로 설계되어야 합니다.경사면은 사용 중에 다시 연마할 필요가 없습니다.중공 드릴 비트의 측면 표면은 재연삭이 가장 쉽고 마모 속도도 가장 빠른 표면입니다.따라서 중공 드릴 비트의 날카로움은 측면 표면을 날카롭게 함으로써 달성됩니다.2차 측면 표면은 내부 2차 측면 표면과 외부 2차 측면 표면으로 구분됩니다.재연삭의 관점에서 볼 때 내측 및 외측 보조 측면을 재연삭하는 것은 쉽지 않으므로 보조 측면은 재연삭되지 않도록 설계해야 합니다.
7.절삭유 및 드릴비트
중공 드릴 비트의 주요 특징은 가공 중에 구멍의 내부 코어가 절단되지 않는다는 것입니다.따라서 중공 드릴 비트의 절단 량은 트위스트 드릴에 비해 훨씬 적고 필요한 드릴링 힘과 절단 중에 발생하는 열도 더 작습니다.고속강 중공 드릴 비트로 드릴링할 때 가공 영역의 온도가 드릴 비트의 경도에 큰 영향을 미치기 때문에 드릴링 공정 중에 냉각수를 사용하여 식혀야 합니다(냉각수를 사용하지 않는 경우 드릴 비트 마모는 주로 상변화 마모이며 초기에는 급격한 마모입니다.처음에는 우리가외부 분무 냉각.그러나 드릴 비트 스테이션은 수평축 방향으로 가공되기 때문에 절삭유가 드릴 비트의 날 부분으로 들어가기 어렵습니다.냉각수 소비량이 많고 냉각 효과가 이상적이지 않습니다.외부 분무 냉각을 내부 분무 냉각으로 변경하기 위해 드릴 장비 스핀들 구조가 재설계되었습니다.절삭유는 중공 드릴 비트의 코어에서 추가되므로 절삭유가 드릴 비트의 절단 부분에 원활하게 도달할 수 있으므로 절삭유 소비가 크게 줄어들고 냉각 효과가 향상됩니다.
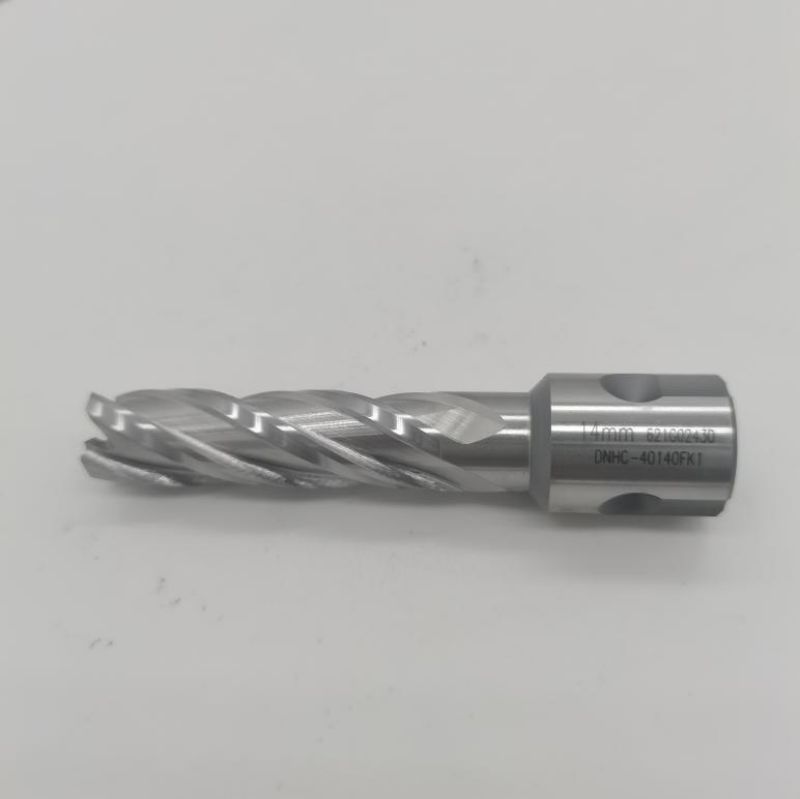
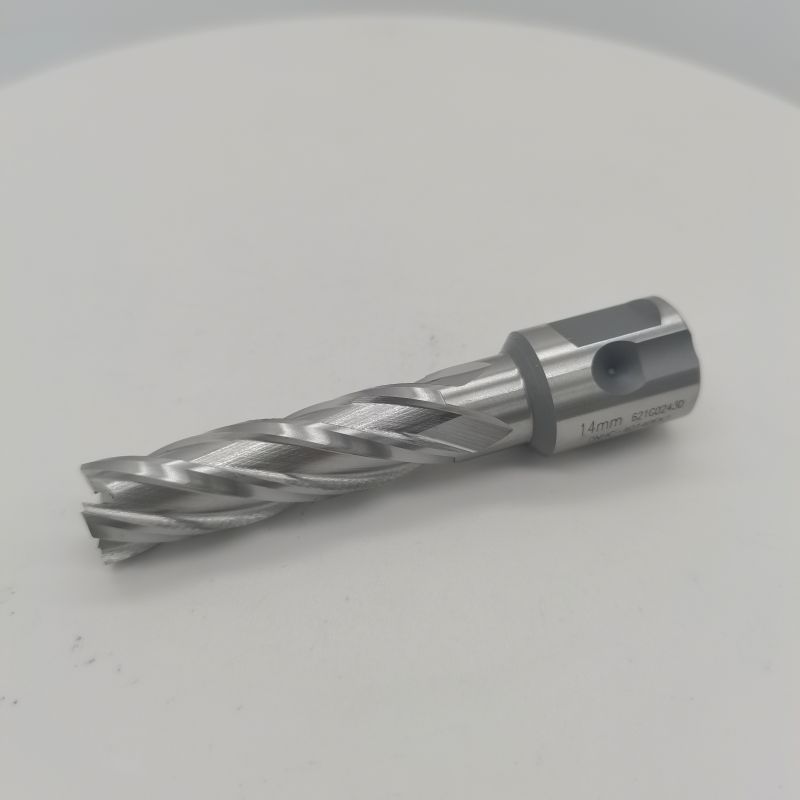
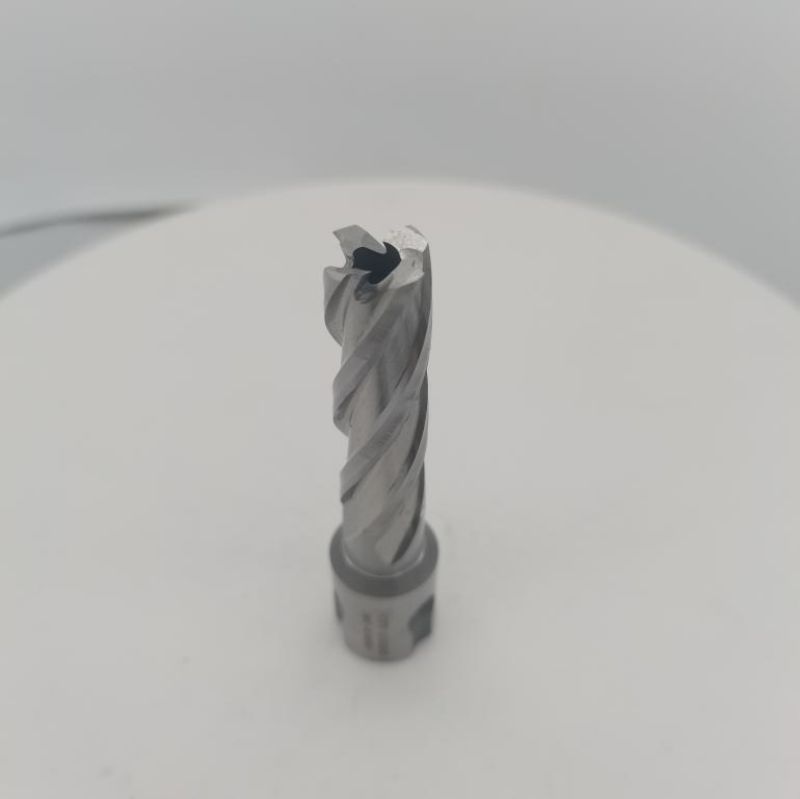